Skills now key to manufacturing jobs
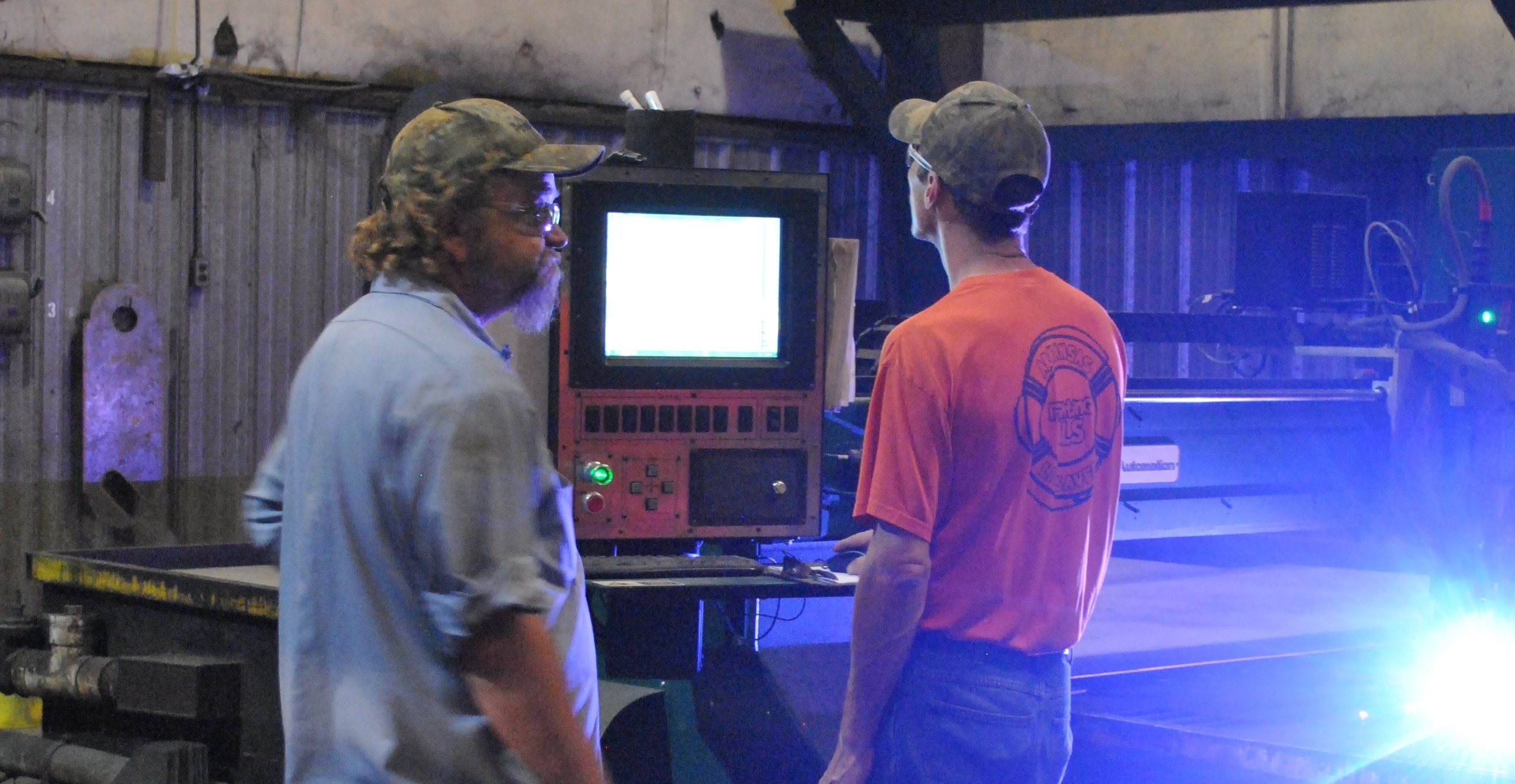
The recession sped what had been a slow decline in Arkansas manufacturing into a free-fall, taking more than 44,000 jobs and changing for many what it means to be a factory worker.
The 22 percent drop in manufacturing jobs, reported by the U.S. Census Bureau, was caused by a mix of decreased demand, outsourcing, increases in efficiency and use of innovative technology throughout the state. Fewer workers are now required to produce the same amount of product.
Those workers are no longer unskilled laborers but experts in science, technology, engineering and mathematics, said Chad Moutray, chief economist at the Washington, D.C.-based National Association of Manufacturers.
“The difference between the U.S. and the other countries is the extent that we use those high-skilled workers to gain higher productivity,” Moutray said. “That requires a completely different worker and a completely different work force.”
In 2011, a National Association of Manufacturers report estimated that as many as 600,000 skilled manufacturing jobs are unfilled in the United States because workers lacked the necessary expertise.
Manufacturers need machinists, operators, craft workers and assemblers with experience. The disparity between need and availability will grow as large numbers of those workers reach retirement age in the next few years.
“The difference is years ago people worked at their houses. Their dads had them building stuff. They were working on cars,” said Mark Burleson, manufacturing manager at Little Rock-based Phelps Fan. “You don’t find as many mechanically inclined people today.”
In Arkansas, manufacturing remains centered in the Forth Smith area, where one in five workers clocks in at a factory, despite a 28 percent drop in factory jobs from 2006 to 2011. That’s the highest concentration of manufacturing workers in Arkansas’ metropolitan areas as defined by the U.S. Census Bureau.
The loss of jobs in the Fort Smith area far outpaced the 22 percent state decline and 19 percent national decline.
The Mercy Fort Smith and Sparks Health Care hospitals expanded in Fort Smith, bringing in more high-paying service sector jobs. But Kermit Kuehn, director of the Center for Business Research and Economic Development at the University of Arkansas at Fort Smith, said a healthcare job gained doesn’t mean the same to the community as a manufacturing job lost.
“It’s like Detroit ignoring a decline in the automobile industry,” Kuehn said. “There’s no way they could ignore that. It’s similar here.”
Since 2011, employment in manufacturing in Arkansas has remained relatively stable, only dropping by about 2,000 workers, according to data from the Bureau of Labor Statistics.
But the decline means more people were employed in health care and social assistance than in manufacturing by 2010, a first for the state.
While manufacturing employment fell, pay was up. Over the same period, salaries increased by 18 percent, from $33,050 to $39,300, according to the U.S. Census Bureau.
In some manufacturing sectors, the changes were more stark. Electrical equipment, appliance and component manufacturing shrank from 14,150 workers to 7,550 workers from 2006 to 2011, but average salary increased 32 percent, from $31,400 to $41,400.
Factors such as inflation and a higher percentage of workers in management affects these numbers, but they also point toward an increased number of high tech workers, said Moutray, the National Association of Manufacturers’ economist.
“The level of skill that’s required for a manufacturing worker today is more than you would expect,” he said.
Walking the factory floor at Phelps Fan is like looking through an old family photo album. Joe Hadden, president of Phelps Fan, and Burleson not only know everyone’s first and last name, but how many years they’ve worked at the plant.
Welder Dennis Freeman will have worked for the nearly 100-year-old Phelps Fan for 36 years on June 15. David Smith, foreman, has been at the factory 42 years.
Burleson said he has given up on finding younger workers who know what they’re doing when they apply. He said he has better luck finding hard workers with solid math skills willing to be trained.
“I give a basic test to incoming people [that includes] fractions, decimals [and] reading a tape measure,” he said. “I’ve never had one person make 100 percent.”
Phelps Fan specializes in custom work that larger manufacturers don’t do. It incorporates an automated plasma cutter that reduces the time it takes to cut metal fan components from more than a day to an hour. Workers upload digital drawings of the components for the machine to cut.
The machine costs about $125,000, but the time it saves makes it worthwhile, Burleson said.
“If there’s a cost benefit to upgrading technology, then we upgrade it,” said Hadden. “We’re probably also welding parts on our fans like they did 100 years ago when they started this company.”
Burleson describes the company’s machinist as more of an artist than a factory worker. He has the skills to make general ideas tangible.
“He’s a true machinist,” Burleson said. “He’s not a machine operator. There’s a big difference. They’re few and far between.”
Dan Curtis, director of Arkansas Manufacturing Solutions, said many small to midsize manufacturers use advanced tools, but full automation isn’t as cost effective as using skilled labor more effectively.
“Manufacturers continually need help making their operations more efficient and opening up capacity,” Curtis said. “For our manufacturers, that’s far more prevalent than automation.”
Manufacturing Solutions focuses on improving efficiency and market opportunities for small to midsize manufacturers in Arkansas.The office is part of a nationwide network of offices partially funded by National Institute of Standards and Technology’s Manufacturing Extension Program.
New skills and increased automation ought to help restore some manufacturing jobs in the Fort Smith area, said Ivy Owen, executive director of the Fort Chaffee Redevelopment Authority.
Whirlpool closed its factory in Fort Smith in 2012. The plant employed about 4,500 workers in 2005. When it closed, fewer than 1,000 people were working there.
“Those heavy industrial jobs that left the United States 10 years ago are not coming back,” Owen said. “People can dream, but we have to retool if we want to remain competitive.”
“I think we’re moving forward,” he said. “There is a light at the end of the tunnel, and that’s technology and retraining.”
Owen said he believes manufacturing has a role in his community.
“The [Whirlpool] building sits there vacant, and in my opinion, it’ll still be sitting there five years after my death,” he said. “My goal is to no longer rely on heavy industry.”
He said companies like Umarex, an air-gun manufacturer, Mars Petcare, and Graphic Packaging are doing well and have been able to increase output with fewer people.
But a $100 million Mitsubishi Power Systems plant that was expected to open in 2012 is vacant because of litigation from competitor General Electric and a declining market in the United States.
Fort Smith’s Kuehn said the area’s economy is changing amid mixed messages from the manufacturing sector.
There are fewer, but more skilled, workers on factory floors. At the same time, employees that previously worked in unskilled positions on the factory floor are forced into the service sector of the local economy.
“The basic trend is higher output and fewer employees,” Kuehn said. “If that job is replaceable with a machine, then you replace it with a machine; otherwise, you export it.”
Kuehn is hopeful for future manufacturing in the area. Domestic energy costs are decreasing because of the abundance of natural gas and wages are increasing far more quickly in Mexico and China than in the United States.
“The amount of investment going into U.S. manufacturing is increasing because the economic formula is shifting back to the U.S.’ favor,” he said. “But it’s not the same type of jobs that are coming back.”
The article was published in The Arkansas Democrat-Gazette on June 2, 2013. To access the article from the newspaper's website, click here. For a .pdf, click here.